Based in Florida
Top 10 Workplace Safety Tips For 2025
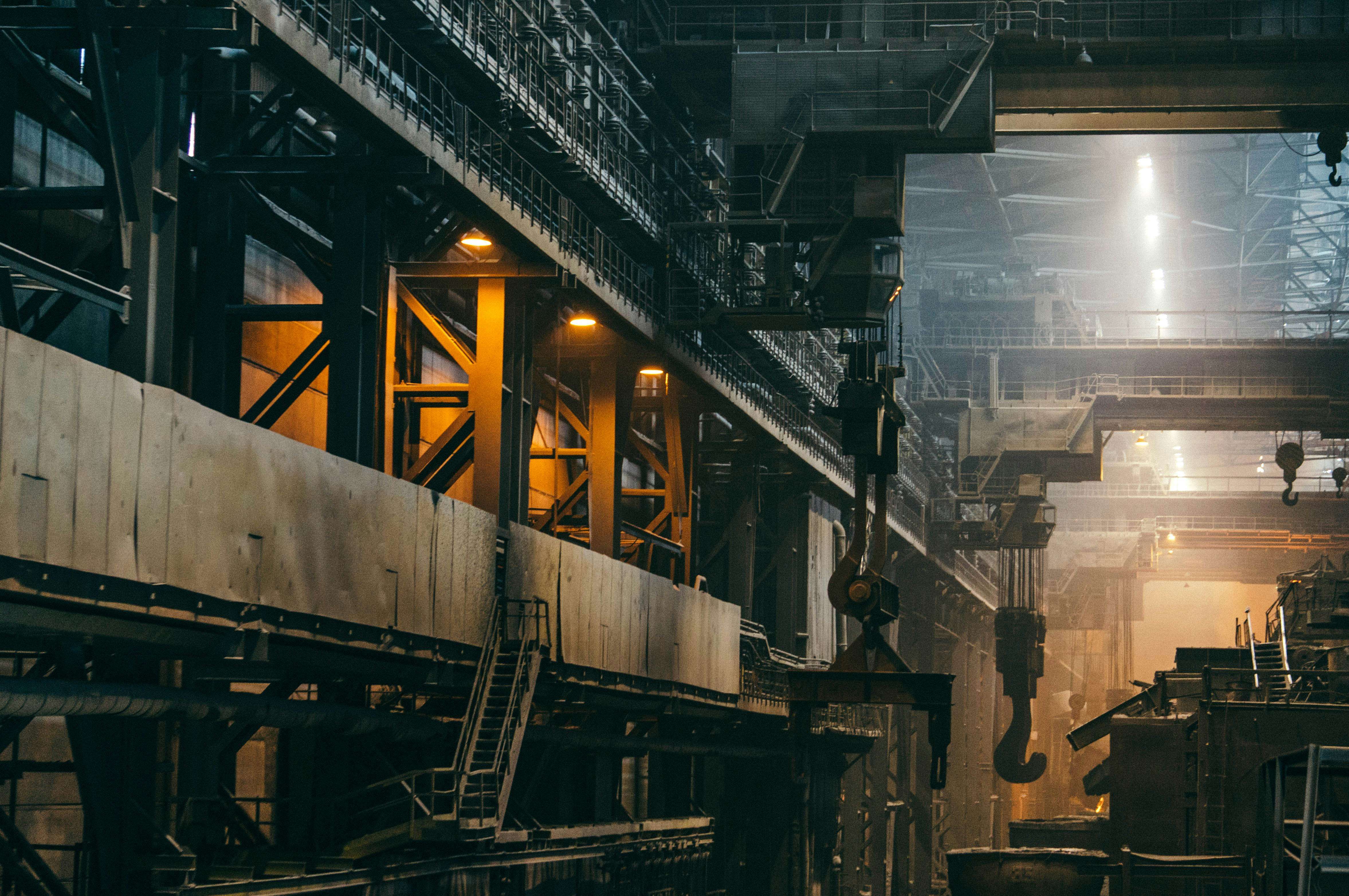
Why Workplace Safety Planning Matters in 2025
Imagine this: you're running a busy job site or manufacturing floor, and suddenly an OSHA inspector walks in unannounced. Are your people prepared? Is your documentation complete? If you're not sure, you’re not alone—and that’s exactly why safety planning in 2025 is not optional.
Safety isn’t a box to check—it’s the heartbeat of your operation.
In 2025, workplace risks are evolving fast. It’s not just slips, trips, and falls anymore. You're now dealing with:
- Hybrid teams and off-site risks
- Heat exposure and climate hazards
- Supply chain interruptions that create unpredictable workflows
- Worker fatigue, stress, and mental health issues
- Regulatory updates that change with little warning
OSHA is ramping up both inspections and fines. Violations that once earned warnings are now leading to hefty penalties. Agencies expect more, and your workforce does too. They want a workplace that protects their health, future, and families.
That’s where Apt Environmental Solutions comes in.
We’re not just safety consultants. We’re your behind-the-scenes EHS team—helping you spot risks before they become problems, and guiding you with practical, proven strategies. We work with you—not just for compliance, but for confidence.
This guide gives you the top 10 safety tips every smart company should act on in 2025.
Whether you're in construction, energy, farming, or manufacturing, these tips are simple, powerful, and built to help your business run safer, longer, and stronger.
Let’s dive in.
Top 10 Workplace Safety Tips for 2025
1. Update Your Safety Program Annually
Your safety program isn't a "set it and forget it" document—it should grow with your company. Updating it annually ensures you’re aligned with the latest OSHA regulations, internal data, and real-world lessons from your past year.
Why it matters
- Regulatory standards shift quickly (e.g., OSHA Heat Illness Prevention Rule expected in 2025)
- Your processes, equipment, and workforce evolve
- Insurance carriers often require current EHS documentation
What to include in your update
- Revise roles and responsibilities for safety teams
- Reassess your emergency response plan
- Review incident logs and corrective actions
- Add training schedules and updated hazard controls
Pro Tip: Assign a recurring calendar event every January for a full safety program review with your EHS lead and department heads.
Real-World Example
One of our manufacturing clients hadn’t updated their LOTO (Lockout/Tagout) procedures in 5 years. After an equipment incident, we discovered outdated processes led to confusion during shutdown. Once Apt reviewed and modernized the plan, incidents dropped by 30% in just 3 months.
2. Conduct Regular Risk Assessments
If you want to prevent workplace injuries before they happen, you must assess risks regularly—not reactively. Think of risk assessments as your EHS playbook. They help you identify hazards, evaluate their impact, and prioritize what needs fixing before someone gets hurt.
Why It Matters
- OSHA mandates hazard assessments under multiple standards (1910.132, 1910.119, etc.)
- Dynamic worksites—like construction zones, oil rigs, and heavy manufacturing—change dailyEquipment upgrades, staffing changes, and new materials often introduce unseen risks
- Insurance providers often request proof of assessments to lower premiums or settle claims
Key Components of a Strong Risk Assessment
- Job Hazard Analysis (JHA): Break down tasks and identify steps where risks occur
- Site Walkthroughs: Regular inspections with your EHS lead and floor supervisors
- Employee Input: Workers often spot hazards that paperwork misses
- Severity x Likelihood Matrix: Prioritize based on real-world risk exposure
- Corrective Actions: Document fixes, timelines, and accountability
Real Example: A mid-sized chemical plant conducted quarterly self-assessments, but incidents kept rising. Apt performed a third-party audit and uncovered 6 high-risk electrical issues overlooked by the internal team. After immediate corrections and training, the plant reported zero incidents over the next 9 months.
Pro Tip: Use a mobile app or digital checklist to track and log hazards in real-time. It improves documentation, enhances accountability, and makes audit prep easier.
Bonus Insight: Don’t just assess physical risks—include ergonomic hazards, repetitive strain tasks, and mental health triggers (like isolation in remote environments or heat fatigue on outdoor crews).
3. Provide OSHA-Compliant Training
Training isn’t a formality. It’s one of the most powerful ways to reduce injuries, boost morale, and meet compliance standards. In 2025, where regulatory expectations and workplace risks continue to evolve, relying on outdated or one-time training won’t cut it.
Why This Matters
- OSHA requires documented, role-specific training under multiple standards (1910.120, 1926.21, etc.)
- Inexperienced and temporary workers are most likely to be involved in preventable incidents
- Poorly trained supervisors often fail to enforce safety policies on the floor
- Fines for missing or outdated training records are among the most common violations
What OSHA-Compliant Training Should Include
- Initial onboarding for all new hires, including part-time and seasonal staff
- Annual refresher training, customized by department or role
- Topic-specific sessions on confined space, fall protection, hazard communication, etc.
- Multilingual delivery to meet the needs of diverse workforces
- Documented participation and retention tracking
Real-World Scenario: A remediation firm working under an OCIP hired several new laborers mid-project. They skipped full training due to tight deadlines. Within two weeks, a trench collapse occurred. Apt was brought in to redesign their onboarding flow, implement task-specific toolbox talks, and document training logs. They’ve since completed three large projects injury-free.
Action Steps
- Review your current training log—if it's older than 12 months, it's time for a refresh
- Schedule monthly toolbox talks led by team leads—not just EHS pros
- Integrate scenario-based drills to build retention, not just compliance
Pro Tip: Training doesn’t stop with a PowerPoint. Use hands-on practice, quizzes, and group walk-throughs to reinforce learning. This is especially important in high-risk industries like construction, energy, and chemicals.
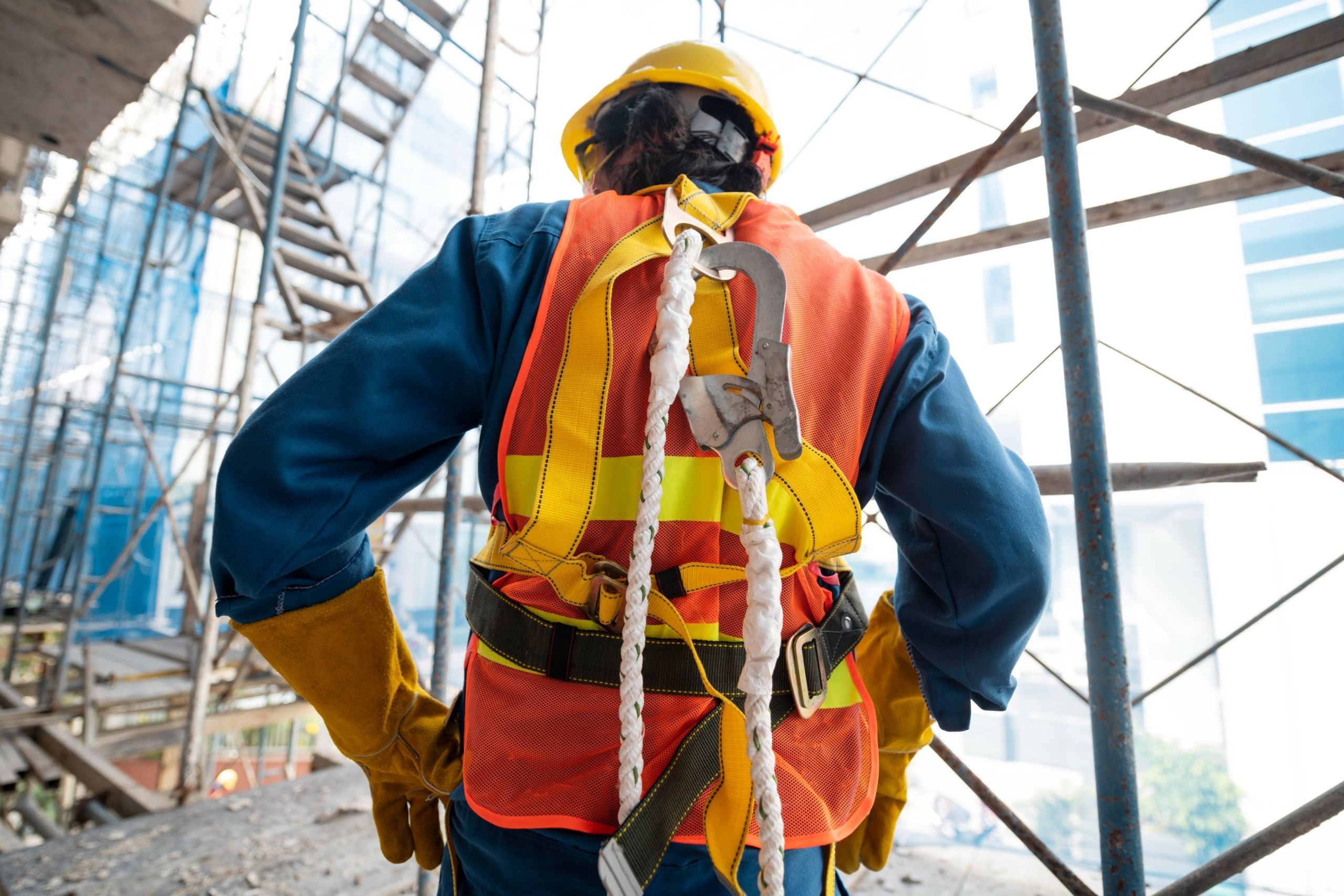
4. Strengthen PPE Protocols
Personal protective equipment (PPE) is your last line of defense—and one of the most overlooked areas in most safety programs. In 2025, strengthening your PPE protocols goes beyond issuing hard hats and gloves. You need to evaluate whether your gear actually fits, works, and protects against the real hazards on your site.
Why This Matters
- OSHA standard 1910.132 requires employers to provide and maintain suitable PPE for identified hazardsImproper PPE use leads to hundreds of preventable injuries annually
- Workers often wear PPE incorrectly or not at all when it's uncomfortable or untested
- Supply chain changes have introduced new, unfamiliar brands and gear into the field
What a Strong PPE Program Includes:
- Hazard-specific PPE selection based on site and task assessments (e.g., silica dust, corrosives, arc flash)
- Proper fit testing for respirators, eye protection, and hearing protection
- Routine inspections and replacement schedules to prevent degraded performance
- Clear signage and access controls at entry points for PPE-required zones
- Training and reinforcement on correct usage, donning/doffing, and maintenance
Real-World Example
An electronics manufacturer used standard masks across departments, including those working near VOC-heavy adhesives. Apt conducted air sampling and found exposure exceeded safe limits. We upgraded their respiratory protection with half-mask cartridges, introduced change-out schedules, and trained floor leads on compliance. VOC complaints dropped, and the company passed its next EPA audit with zero findings.
Action Steps
- Conduct a PPE audit across departments—what’s being used, how, and by whom
- Remove expired, damaged, or non-certified gear from circulation
- Schedule quarterly PPE reviews to adjust for seasonal or task-specific needs
Pro Tip: Don’t assume PPE is being used just because it’s on-site. Build PPE checks into supervisor routines and include usage observations in your daily safety walks.
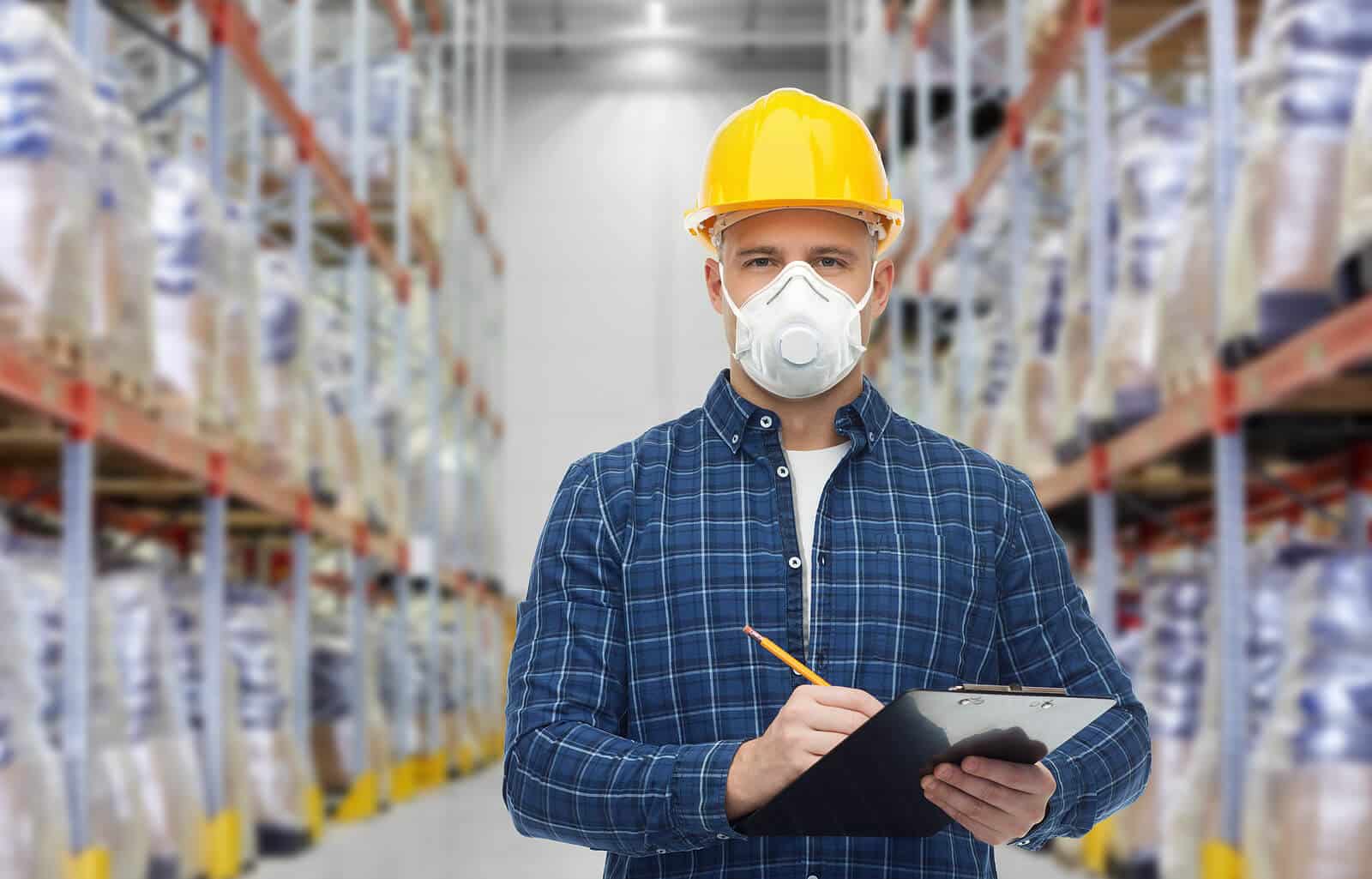
5. Establish a Reporting Culture
Most safety programs fail not because hazards go unseen—but because no one reports them. A strong reporting culture turns your frontline workers into your most valuable safety asset. It shifts the mindset from blame to prevention, encouraging everyone to speak up before something goes wrong.
Why This Matters
- According to the National Safety Council, 75% of serious incidents are preceded by a near-miss that went unreported
- OSHA emphasizes hazard reporting as a core part of an effective injury and illness prevention program (IIPP)
- The more near-misses and unsafe conditions you track, the fewer serious incidents you’ll face
- A transparent reporting culture builds trust and reinforces accountability at every level
Signs Your Reporting Culture Needs Work
- Workers only report issues after incidents occur
- Near-miss logs are empty—or non-existent
- Employees are afraid to report hazards due to fear of blame or retaliation
- Safety meetings are one-way conversations instead of two-way discussions
How to Build a Strong Reporting Culture
- Make reporting easy with digital forms, anonymous options, or a QR code in break rooms
- Praise reporting—not just outcomes. Celebrate the act of noticing and sharing hazards
- Train supervisors to respond constructively to reports and follow up fast
- Close the loop by sharing what actions were taken after reports come in
- Track trends from reports to find systemic issues before they escalate
Real-World Example
A construction client working under an OCIP program had zero near-miss reports for months—until a fall nearly occurred. Apt introduced behavior-based safety observations and trained foremen on report coaching. Within 60 days, near-miss reports increased 5x, and minor incident rates dropped 40%.
Action Steps
- Start every safety meeting with a recent report and what changed because of it
- Designate a weekly “Safety Hero” who reported a key issue—recognition works
- Integrate reporting KPIs into supervisor performance metrics
Pro Tip:Use a mobile-friendly system to capture and categorize reports in real time. Include fields like location, task, risk severity, and suggested fix.
6. Monitor Air Quality and Noise Exposure
Not all hazards can be seen or touched. Some of the most dangerous threats to worker health—like fine dust, volatile chemicals, and constant machine noise—are invisible and often ignored. That’s why regular air and noise monitoring isn’t optional—it’s essential to keeping your people safe and your business compliant.
Why This Matters
- Long-term exposure to hazards like silica, VOCs, carbon monoxide, and industrial noise leads to chronic illnesses
- OSHA, NIOSH, MSHA, and EPA all have enforceable exposure limits
- Many workplaces are unaware they’ve exceeded limits until an inspection—or a health complaint
- Workers may not report symptoms early due to fear of job loss or lack of awareness
Common Risk Environments
- Manufacturing and electronics (solvents, solder fumes, VOCs)
- Mining and quarries (dust, silica, diesel exhaust)
- Construction sites (cutting concrete, enclosed space fumes)
- Industrial kitchens or facilities with poor HVAC flow
- Any site using chemicals or loud power tools
What Monitoring Should Include
- Air sampling for particulates, gases, vapors, and fumes using NIOSH or EPA-approved methods
- Noise dosimetry to measure employee exposure throughout the shift
- Personal exposure monitoring for high-risk roles (e.g., welders, mixers, grinders)
- Review of SDS sheets and proper ventilation based on chemical use
- Health surveillance for hearing loss, respiratory issues, and more
Real-World Example
A quarry operation contacted Apt after several workers complained of dizziness and fatigue. Our team conducted full-shift air and noise monitoring. We identified dangerously high silica levels near the primary crusher and unsafe noise exposure above 90 dB. After installing dust control and issuing dual-protection hearing gear, silica exposure dropped by 60%, and MSHA passed the site with no citations.
Action Steps
- Schedule baseline testing now, especially if it’s been over a year
- Use test results to update your PPE, training, and engineering controls
- Repeat monitoring after major process or equipment changes
Pro Tip:Use results from monitoring to drive employee education. When workers understand what they’re breathing—and how to protect themselves—they engage more with PPE and protocols.
7. Prepare for Emergencies with Updated Plans
Emergencies don’t schedule themselves. Fires, chemical spills, severe weather, and active threats can hit without warning. If your team doesn’t know what to do in the first 60 seconds, the consequences can multiply—fast. That’s why emergency planning isn’t just about compliance—it’s about survival.
Why This Matters
- OSHA requires written emergency action plans (EAPs) under 29 CFR 1910.38
- Inconsistent or outdated plans are a top cause of panic, confusion, and injuries during incidents
- Emergency plans that exist only on paper—or haven’t been tested—won’t help in a real crisis
- Emergency response failures can lead to lawsuits, lost contracts, and damaged reputations
What Every Emergency Plan Should Include
- Site-specific evacuation procedures based on building layout and task hazards
- Chain of command with clear roles and responsibilities (who calls, who leads, who shuts down equipment)
- Communication plan for alerting employees, contractors, and first responders
- Response protocols for fires, spills, severe weather, chemical releases, and workplace violence
- Drill schedule to practice the plan and identify gaps (at least once per year)
- Accessible versions of the plan—posted in work zones and mobile-friendly
Real-World Example
A packaging facility working with flammable materials hadn’t updated their emergency response procedures in over five years. When a small fire broke out near the storage area, confusion led to a delayed evacuation—and three minor injuries. Apt was brought in to redesign their plan, run evacuation drills, and integrate a mass alert system. The next year, a similar fire was contained and evacuated within minutes, with no injuries.
Action Steps
- Review your plan quarterly, especially after operational or staffing changes
- Make sure all new hires are trained on emergency procedures in their first week
- Coordinate with local fire, EMS, or hazmat teams to ensure they’re familiar with your site
Pro Tip: Add emergency plan testing to your safety calendar—and use unannounced drills to build real-world readiness. After each drill, conduct a debrief to identify what went well and what needs improvement.
8. Review Contractor Safety Requirements
When a contractor steps onto your job site, their risk becomes your responsibility. Without clear expectations and a consistent screening process, one mistake by a subcontractor can lead to injuries, shutdowns, or OSHA violations—and you’re the one liable.
Contractor safety isn’t just about paperwork. It’s about building a system where every person on-site—employee or not—follows your safety standards from day one.
Why This Matters
- OSHA holds host employers accountable for unsafe contractor behavior under the Multi-Employer Citation Policy
- Owner-Controlled Insurance Programs (OCIPs) often require strict contractor safety oversight
- Most severe jobsite incidents involve third-party labor, not full-time employees
- Inconsistent contractor safety practices can erode site culture and delay schedules
What a Strong Contractor Safety Program Includes
- Prequalification screening: Require safety history, insurance verification, EMR rates, and program documentation
- Onboarding orientation: Deliver site-specific hazard training before work begins
- Daily check-ins: Confirm work scope, hazards, and PPE compliance before entry
- Supervision expectations: Define who is responsible for monitoring contractor behavior
- Performance tracking: Monitor safety KPIs and document violations or near misses
Real-World Example
A $120M remediation site managed under an OCIP had over a dozen subcontractors, each with different policies and training levels. After several close calls, Apt implemented a centralized prequalification system, bilingual orientations, and daily contractor audits. The result: 14 months with zero OSHA-recordable incidents and a compliant safety record across all trades.
Action Steps
- Audit your current contractor management process: Are you screening and tracking every crew?
- Develop a safety packet and orientation checklist all vendors must complete before arrival
- Schedule joint safety walks between contractors and your site EHS lead
Pro Tip: Don’t assume contractors follow your standards. Assign a supervisor or safety coordinator to conduct daily spot checks and document compliance. This small step builds accountability and protects your liability.
9. Use Technology to Track Incidents & Training
Paper logs and spreadsheets won’t cut it anymore—not when you’re juggling multiple sites, workers, and compliance standards. The right safety tech helps you track incidents, monitor training, and stay audit-ready, all without losing hours to admin work.
Digitizing your EHS processes isn’t just about convenience. It’s about reducing risk, increasing visibility, and showing regulators that you take safety seriously.
Why This Matters
- OSHA requires accurate recordkeeping of incidents (OSHA 300, 301, 300A)
- Missed training logs are one of the top reasons for OSHA citations
- Manual processes often delay corrective actions or result in missed deadlines
- Real-time data helps spot safety trends before they lead to serious incidents
What Smart Safety Tech Can Do
- Log and categorize incidents or near misses from any device
- Send automated reminders when training or certifications are due
- Store SDS, SOPs, and emergency contacts in one place—accessible from any jobsite
- Generate audit-ready reports instantly
- Track toolbox talks, attendance, and task-specific safety briefings digitally
Real-World Example
A manufacturing client was using paper checklists and binders for all safety tracking. They regularly missed annual training deadlines and couldn’t produce documentation during surprise inspections. Apt helped them implement a cloud-based EHS system with mobile logging and auto-reminders. Within 90 days, they had 100% compliance across six departments—and 75% less time spent on paperwork.
Action Steps
- Identify your biggest admin bottlenecks: Is it tracking training? Finding past incident reports?
- Choose an EHS software or platform that fits your team’s size and tech comfort level
- Train supervisors on how to use the system and review reports weekly
Pro Tip: Start small. Begin with digital incident logs or training checklists, then expand. Focus on tools that allow real-time access from mobile devices—it’s a must for field teams and construction crews.
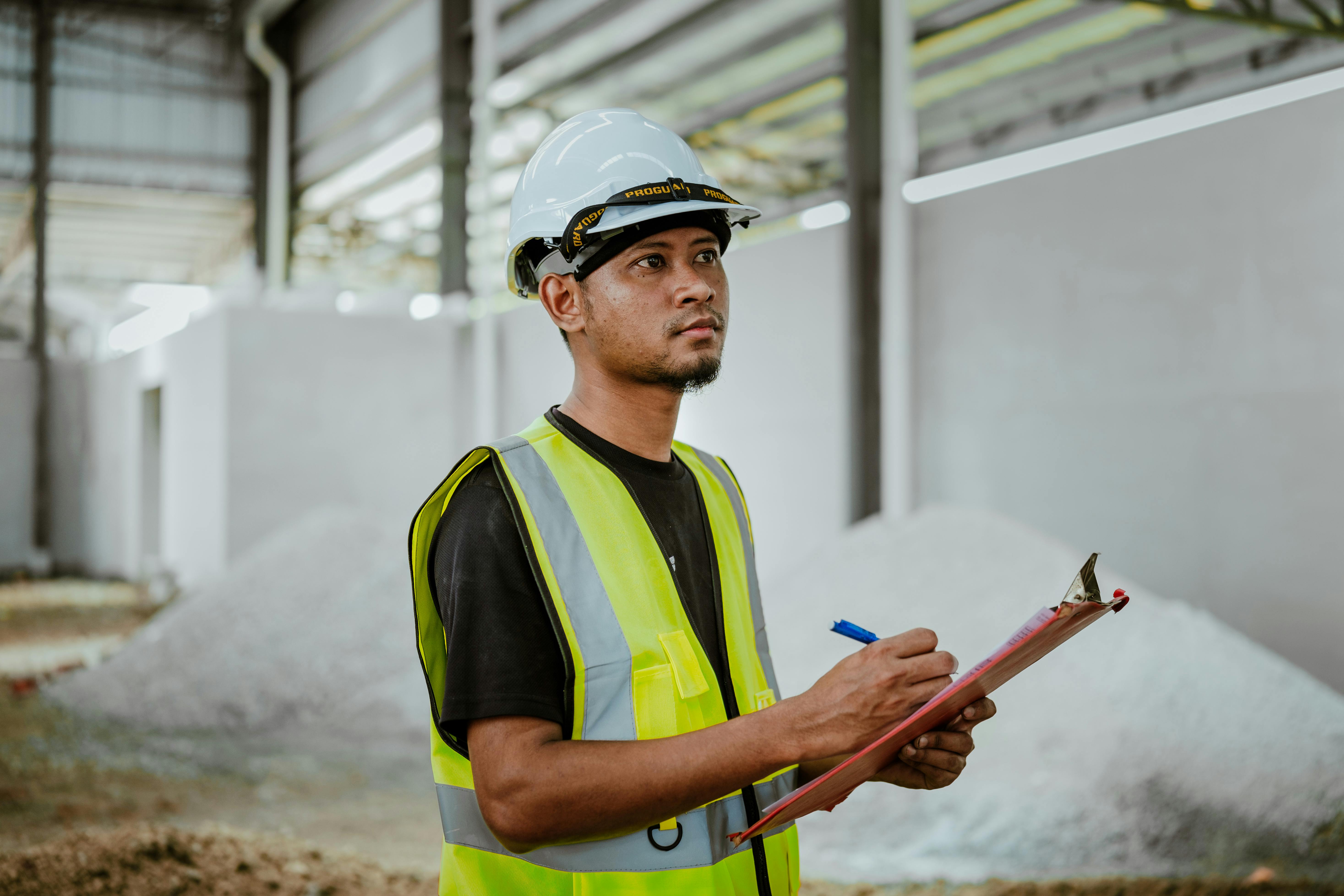
10. Audit for WPS, PSM, or Tier II Requirements
Some industries don’t just need a general safety plan—they require strict compliance with specialized federal programs like the Worker Protection Standard (WPS), Process Safety Management (PSM), and Tier II chemical inventory reporting. These aren’t optional. If you fall under these rules, routine audits are essential to protect your people, your permits, and your reputation.
Why This Matters
- The EPA and OSHA both impose heavy fines for non-compliance with WPS, PSM, and Tier II
- Many companies fail inspections due to outdated SOPs, poor documentation, or staff turnover
- These programs are often forgotten until an audit is scheduled—or a major incident occurs
- Tier II reports must be submitted annually and accurately reflect on-site chemical inventories
Who This Applies To
- Agricultural operations that apply or store pesticides (WPS)
- Chemical manufacturers or processors handling highly hazardous substances (PSM)
- Any facility storing certain thresholds of regulated chemicals (Tier II)
What a Compliance Audit Should Include
- Gap analysis of your current SOPs, emergency plans, and training logs
- Inventory check of all regulated chemicals on-site
- Employee interviews to test actual knowledge vs. documented procedures
- Labeling and signage review across storage areas and application zones
- Mock audit or drill to evaluate response time and documentation retrieval
Real-World Example
A mid-sized resin plant contacted Apt after failing an internal PSM audit. We discovered multiple SOPs hadn’t been updated in over four years, and SDS documentation was incomplete. Our team overhauled their entire system, digitized chemical tracking, and provided supervisor training. The result? A 98% score on their follow-up OSHA PSM audit—and zero violations.
Action Steps
- Review which standards apply to your site (WPS, PSM, Tier II)
- Schedule an internal or third-party audit before your next regulatory deadline
- Document every change and corrective action in a centralized system
Pro Tip: Don’t wait for a letter from OSHA or the EPA. Set a compliance calendar for recurring audits—ideally at least 3 months before your Tier II due date (March 1st in most states).
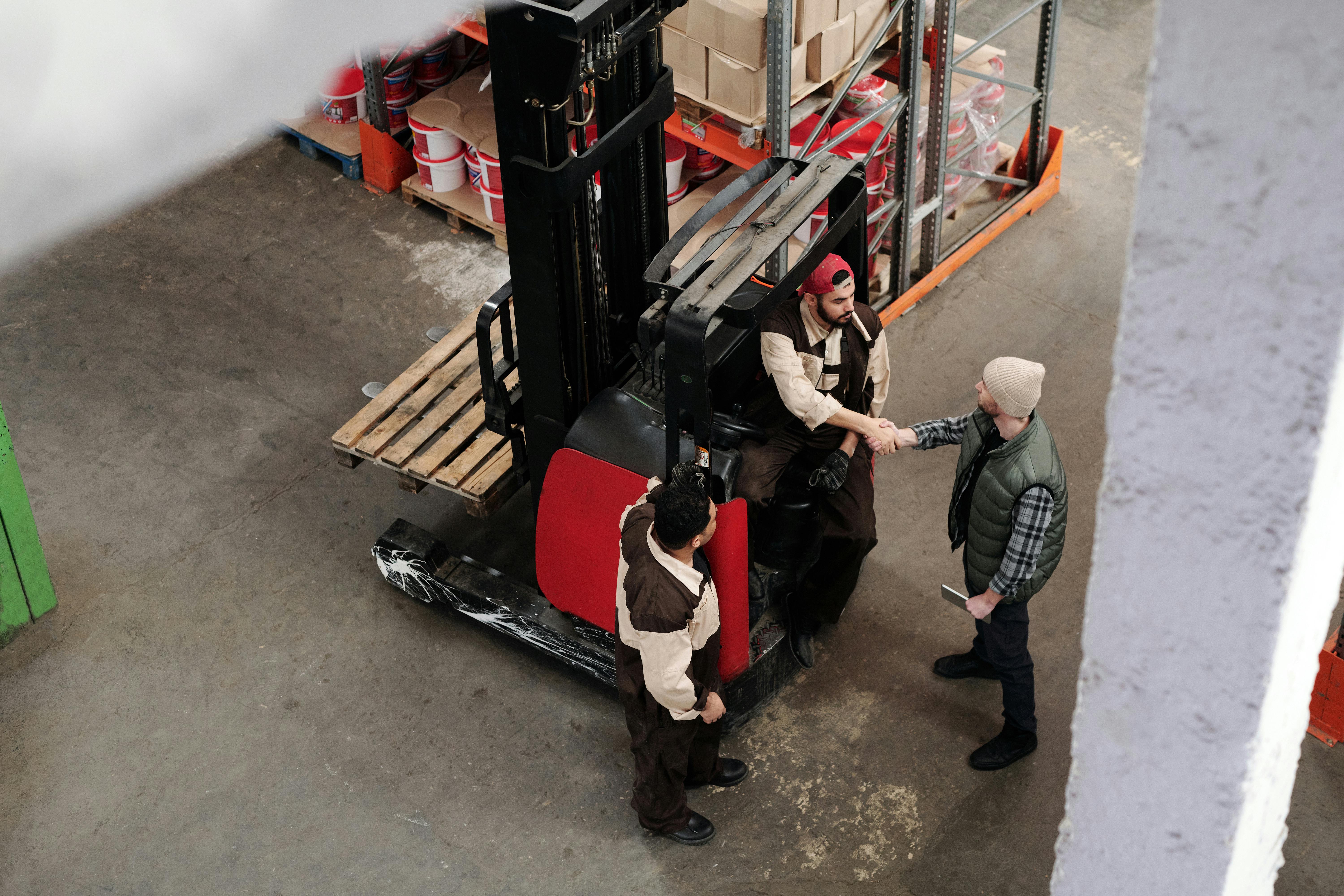
Ready to Strengthen Your Safety Program in 2025?
Workplace safety doesn’t happen by luck—it happens by leadership.
Whether you’re managing a construction crew, a processing plant, or a farming operation, the risks your team faces are real. Regulations change, processes evolve, and expectations rise. But with the right plan, the right partner, and the right tools, you can build a safer, stronger, and more compliant work environment—one step at a time.
At Apt Environmental Solutions, we’ve helped clients across industries reduce incidents, pass inspections, and boost confidence—without slowing down operations. From risk assessments to emergency planning, from industrial hygiene to contractor oversight, we become part of your team.
Need help updating your safety program?
Preparing for an audit or inspection?
Looking for a training or compliance partner?
Let’s talk.
Call Us: 1-360-299-6666
Email: info@aptsol.net
Request a Free Safety Consultation
Explore More
- Occupational Safety Management Services
- Workplace Safety Checklist (Free Download)
Case Study: 14 Months Injury-Free on a $120M Construction Project
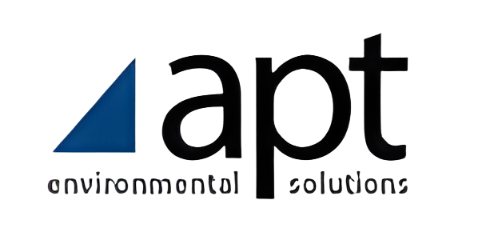
Get in touch