Based in Florida
How to Conduct a Successful Environmental Audit
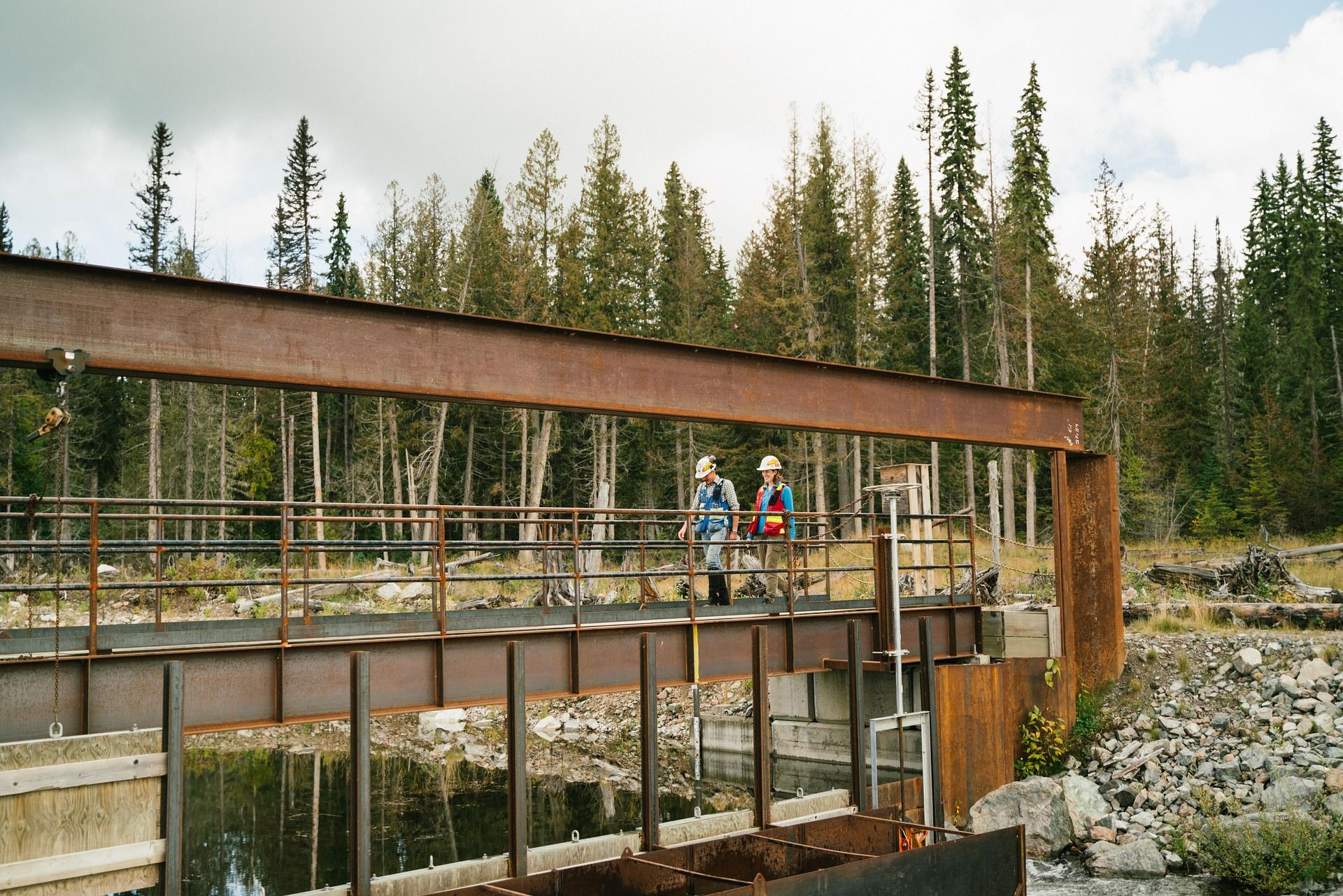
Why Environmental Audits Are Critical
Think your facility’s running clean? You won’t know until you check.
That’s exactly what an environmental audit does—it gives you the full picture. Not just what looks good on paper, but what’s really happening on the ground. These audits examine how well your business follows environmental laws, industry standards, and internal policies. And in today’s world, that matters more than ever.
What Is an Environmental Audit?
An environmental audit is a structured review of your site’s environmental performance. It checks whether you’re complying with government rules (like those from the EPA), managing your risks properly, and keeping your permits, plans, and people in line.
But it’s not just about avoiding penalties. It’s about protecting your brand, your workers, and your future.
Who Needs Environmental Audits?
Whether you’re running a factory, breaking ground on a construction site, or managing a farm or commercial building, if your business generates waste, handles chemicals, or interacts with air, water, or land—you need audits.
Here are just a few examples
- Manufacturing facilities dealing with VOCs, wastewater, or hazardous materials
- Agricultural operations that store or apply pesticides
- Chemical plants regulated under EPA and OSHA standards
- Construction firms with stormwater permits or soil disruption
- Real estate developers needing Phase I or II site assessments
If your facility has pipes, drains, drums, fuel tanks, HVAC systems, or even a dusty parking lot—you're on the radar.
Why Now? Enforcement and Expectations Are Changing
- EPA fines are rising. In 2023 alone, EPA issued over $200 million in penalties for environmental violations. That number is climbing.
- State regulators are stepping up too, especially in California, Texas, Washington, and New York.
- ISO 14001 and ESG standards are driving more audits from investors and internal compliance teams.
- Companies are being pushed to prove—not just say—they’re environmentally responsible.
Environmental audits help you get ahead of the issues. Instead of reacting to violations or complaints, you find problems early, fix them fast, and build confidence across your team and stakeholders.
Why Apt Environmental Solutions?
At Apt, we don’t just perform audits. We partner with your team to uncover real risks, simplify complex rules, and help you fix what matters. We’ve helped hundreds of facilities across energy, chemicals, manufacturing, construction, and agriculture stay compliant, pass inspections, and avoid shutdowns.
Understand the Types of Environmental Audits
Not all environmental audits are the same. Different industries, facilities, and situations call for different approaches. If you're unsure which type applies to your operation, here's a breakdown of the four main categories you need to know—each with its own purpose, process, and impact.
1. Compliance Audits
Purpose: To verify that your facility is following all environmental laws and permit conditions.
These audits focus on your alignment with federal, state, and local regulations—including EPA requirements, Clean Water Act rules, Clean Air Act permits, hazardous waste handling (RCRA), and more. If you're discharging water, managing waste, using regulated chemicals, or operating machinery that produces emissions, this is the audit you can’t afford to skip.
You’ll need this if
- You’re subject to EPA or state environmental inspections
- You hold air, water, or waste permits
- You want to identify and fix non-compliance before enforcement action hits
Outcome: A detailed report showing where you comply and where you’re exposed—plus corrective action recommendations.
2. Management System Audits
Purpose: To check how well your internal systems support environmental performance.
These audits evaluate your organization’s alignment with ISO 14001 (Environmental Management Systems) or ISO 45001 (Occupational Health & Safety Management). They focus less on direct violations and more on how your policies, documentation, and workflows support sustainability and risk management.
You’ll need this if
- You're pursuing or maintaining ISO certification
- Your stakeholders or board require ESG reporting
- You’re focused on continuous improvement and want a structured system
Outcome: A scorecard showing the maturity of your system and how to improve.
3. Due Diligence Audits (Environmental Site Assessments)
Purpose: To assess environmental risk before buying, leasing, or developing a property.
Due diligence audits—often called Phase I or Phase II Environmental Site Assessments (ESAs)—are common in real estate, construction, and acquisitions. Phase I looks at historical site use and red flags. Phase II involves actual sampling of soil, groundwater, or building materials.
You’ll need this if
- You’re buying or refinancing a commercial or industrial property
- You need protection under the “innocent landowner” defense (CERCLA)
- You’re developing on land that may have contamination history
Outcome: A legal record that helps you identify liabilities, negotiate pricing, or secure financing.
4. Internal vs. Third-Party Audits
What’s the difference?
- Internal audits are performed by your in-house team. They're helpful for routine checks or training purposes.
- Third-party audits are done by outside experts like Apt Environmental. These bring objectivity, industry knowledge, and regulatory expertise.
Why third-party audits are often better:
- Regulators and insurers trust them more
- They reveal blind spots your team may overlook
- They reduce bias and internal pressure during evaluations
Pro Tip: Even if you do regular internal audits, consider a third-party audit once a year to catch bigger risks and stay ahead of enforcement trends.
Summary Table: Types of Environmental Audits
Audit Type | Best For | Common Users |
---|---|---|
Compliance Audit | Meeting EPA/state laws, permit reviews | Manufacturing, chemical, energy |
Management System | ISO certification, ESG tracking | Corporate, large facilities, exporters |
Due Diligence | Real estate deals, brownfield redevelopment | Developers, investors, contractors |
Internal vs. 3rd Party | Routine check-ins vs. full external reviews | All industries |
Pre-Audit Preparation Checklist
Before you start an environmental audit, preparation is everything.
The better you plan, the smoother the process—and the fewer surprises you’ll face when the audit begins. Whether you're conducting a compliance review, an ISO gap analysis, or a Phase I site assessment, this checklist will help you get your team and your documentation ready.
Think of this as your audit launchpad.
Step-by-Step Audit Prep Guide
1. Assign an Audit Lead
Choose someone to take points. This person should:
- Understand your facility’s operations
- Be familiar with environmental permits and procedures
- Have the authority to gather documentation and coordinate team responses
Tip: If using a third-party auditor, choose someone internal to shadow and support.
2. Gather Key Documents
Before the walkthrough, collect and organize
- Environmental permits (air, water, stormwater, waste)
- Hazardous waste manifests and disposal records
- Spill prevention and emergency response plans
- Safety Data Sheets (SDS) for all chemicals
- Training logs (HAZWOPER, RCRA, stormwater, etc.)
- Inspection and maintenance records
- Previous audit reports or violation notices
- Waste storage maps and floor layouts
Create a digital audit binder so everything is easy to access on-site or remotely.
3. Notify Departments and Staff
Let your teams know when the audit will happen, what to expect, and how they’ll be involved. This improves:
- Cooperation during site walkthroughs
- Awareness of where documentation is stored
- Readiness for interviews or spot checks
Good communication reduces delays and confusion during the audit.
4. Review Past Issues and Corrective Actions
If you've had previous audits, inspections, or violations, go back and:
- Check whether all corrective actions were completed
- Document proof of closure (emails, reports, photos, sign-offs)
- Highlight improvements made since the last review
This shows progress and builds trust with regulators or auditors.
5. Train Staff on Audit Basics
Train front-line workers and supervisors on
- Who the auditor is and what they’ll be doing
- What to say (and not say) during interviews
- Where emergency equipment and SDS are located
- How to report concerns or ask questions
Even 30 minutes of training can make a big difference in how your team performs during the audit.
6. Conduct a Mock Audit
Walk your site with an internal team (or Apt Environmental) and look for:
- Leaking containers or unlabeled drums
- Unsecured secondary containment
- Expired permits or outdated emergency contact sheets
- Incomplete inspection logs or training gaps
Catching small issues before the real audit helps you avoid formal citations or costly corrections.
Conducting the Site Walkthrough
The site walkthrough is where your audit moves from the page to the floor.
This is when the auditor (internal or third-party) visually inspects your facility, speaks with employees, checks for red flags, and verifies what your documentation claims. What they find here will directly impact your final report—so it pays to prepare and walk through it with a plan.
What the Walkthrough Is For
- Confirming that environmental practices match your written procedures
- Identifying unsafe conditions or potential violations
- Observing how waste, emissions, and chemicals are managed in real time
- Speaking with workers to gauge awareness and culture
What Areas Should Be Inspected?
Auditors will usually focus on high-risk areas, including:
Hazardous Waste Storage Zones
- Are containers labeled, sealed, and dated?
- Is secondary containment in place?
- Are incompatible materials stored separately?
Stormwater and Drainage Points
- Are outdoor materials covered?
- Are discharge locations free of debris and staining?
- Is your SWPPP (Stormwater Pollution Prevention Plan) being followed?
Air Emissions Sources
- Are ventilation and control equipment operating properly?
- Are logs for filter changes and maintenance up to date?
Chemical Storage Areas
- Are SDS available and accessible?
- Are flammable or corrosive materials segregated correctly?
Production and Processing Lines
- Are materials being handled according to SOPs?
- Are emergency shutoffs and spill kits visible and working?
Waste Accumulation Points
- Are accumulation dates within regulation?
- Are logs current and accurate?
Employee Work Zones
- Do staff understand PPE, emergency exits, and hazard signs?
- Can they explain how to report spills or concerns?
Best Practices During the Walkthrough
- Take detailed notes. Write down what you see—not just what’s wrong, but what’s working.
- Capture photos. Document issues and compliance visually (but avoid photos of employees’ faces without permission).
- Stay objective. Don’t make excuses or downplay findings—record the facts.
- Ask questions. Talk to team members, not just managers. They often spot problems earlier.
- Follow your checklist. Don’t rely on memory. Structured tools help ensure consistency.
Real-World Example:During a routine walkthrough at a chemical blending facility, Apt identified an unlabeled 55-gallon drum stored outside with no secondary containment. The contents? Flammable solvent. The issue was corrected immediately—but had an EPA inspector found it first, the fine could have exceeded $20,000.
Key Tip:Treat your walkthrough like a story—what’s happening from raw material entry to waste disposal. If anything breaks that clean, compliant flow, it’s a red flag.
Common Audit Findings & How to Address Them
Most environmental audits uncover some form of non-compliance. That doesn’t mean your operation is failing—it means there’s room to improve. The key is to catch small issues before they become big violations.
This section walks you through the most common findings we see at Apt Environmental—and what you can do right now to correct or prevent them.
1. Improper Hazardous Waste Labeling
The Problem Drums, containers, or tanks missing required labels like accumulation start dates, chemical names, hazard class, or the words “Hazardous Waste.”
Why It Matters Improper labelling is one of the top EPA and state citation causes. It shows a lack of control and puts workers and emergency res ponders at risk.
How to Fix It
- Use durable, weatherproof labels
- Include full chemical names (not abbreviations)
- Train staff on when and how to label
- Conduct weekly container inspections and log them
2. Expired or Missing Permits
The Problem Your air, storm water, or waste permits are out of date—or missing altogether.
Why It Matters Operating without an active permit is a serious violation that can lead to shutdowns or legal action.
How to Fix It
- Assign a compliance calendar to track expiration dates
- Work with a qualified environmental consultant to manage renewals
- Store digital and physical copies of every permit on-site and accessible
3. Poor Recordkeeping
The Problem You can’t find disposal manifests, training records, inspection logs, or corrective action documentation during the audit.
Why It Matters If you can’t prove it, it didn’t happen. Regulators need written evidence to verify compliance.
How to Fix It
- Go digital: use cloud-based tools to store records securely
- Schedule quarterly file reviews to ensure logs are up to date
- Create checklists for every required document category
4. Incomplete Storm water or SPCC Plans
The Problem Your facility lacks a current SWPPP (Storm water Pollution Prevention Plan) or SPCC (Spill Prevention, Control, and Countermeasure) plan.
Why It Matters These plans are required under the Clean Water Act for many facilities and are often the first thing inspectors ask to see.
How to Fix It
- Conduct a site drainage and spill risk survey
- Update your SWPPP or SPCC plan every 3 years—or when operations change
- Train employees on spill response roles and equipment locations
5. Untrained Staff
The Problem Operators and technicians aren’t familiar with safety protocols, waste handling procedures, or emergency actions.
Why It Matters Training is a regulatory requirement—and your strongest defense in case of an incident.
How to Fix It
- Hold annual training on RCRA, stormwater, and chemical handling
- Track attendance and test understanding
- Post emergency contacts and signage in visible areas
Real-World Insight: In a recent audit at a commercial facility, Apt found dozens of drums stored indoors without labels or secondary containment. While operations were clean, the labeling gaps could’ve cost thousands in fines. Within 10 days, we helped them re-label, reorganize, and log every container—and they passed their follow-up inspection with zero findings.
Key Takeaway: Most audit issues come down to lack of documentation, training, or oversight. Fixing them early protects your team, your reputation, and your bottom line.
Post-Audit: Reporting and Corrective Actions
An audit doesn’t end when the walkthrough is over. In fact, the most important work begins after the auditor leaves. The goal isn’t just to identify gaps—it’s to fix them. Fast, thoroughly, and with clear documentation.
This section shows you how to take your findings and build a plan that improves compliance, reduces risk, and strengthens your operation long-term.
1. Review and Organize the Audit Report
Once the audit is complete, you’ll receive a written report (if done by a third party) or your team’s internal findings. It should include:
- A summary of strengths and gaps
- Specific observations tied to regulations
- Photos or documentation of concerns
- A risk level (high, medium, low) for each issue
What to do next
- Review the report with your leadership and EHS team
- Ask questions to clarify any unclear findings
- Acknowledge serious issues that require immediate action
2. Prioritize Findings by Risk
Not every finding is equal. Focus first on high-risk issues that could lead to environmental harm, fines, or worker safety threats. Then work down to lower-risk concerns.
Example risk categories
- High: Unlabeled hazardous waste, expired permits, uncontrolled discharges
- Medium: Incomplete training records, outdated SDS binders
- Low: Missing signage, minor procedural lapses
Tip: Use a corrective action matrix to assign deadlines and owners for each item.
3. Assign Responsibilities and Set Deadlines
Make sure each corrective action has:
- A clear owner (not “the team”—a person)
- A deadline
- Any support needed (vendor, budget, training)
Use a shared tracker so all updates and completion dates are visible. Regularly check progress in safety or leadership meetings.
4. Document Every Fix
For every issue you resolve, save proof. Regulators want to see not just what you found—but how you fixed it.
Documentation examples
- Before-and-after photos of repairs
- Training sign-in sheets and presentations
- Updated policies or SOPs
- Purchase orders for spill kits, signs, or containers
Why it matters: This documentation can protect you during enforcement inspections and show good-faith efforts to improve.
5. Notify Agencies if Required
If your audit uncovers a reportable issue (like an unauthorized discharge or permit violation), you may need to notify the EPA, state agency, or local authority.
Best practice: Don’t wait. Report promptly, explain the fix, and show documentation.
Working with an expert like Apt can help you report correctly and minimize legal risk.
Real-World Example: After an environmental audit revealed expired air permits and missing disposal manifests, a client in the manufacturing sector worked with Apt to organize, renew, and digitize all required files. Within 30 days, they completed 100% of action items and passed a surprise follow-up state inspection—no fines, no warnings.
Final Tip: Turn the Report Into a Roadmap
Treat your audit findings like a to-do list—not a judgment. When used right, an audit becomes one of your best tools for building a safer, cleaner, and more compliant operation.
How Apt Helps Companies Stay Audit-Ready
An audit doesn’t need to be stressful—when you have the right partner. At Apt Environmental Solutions, we go beyond checklists. We help you build systems that work, teams that are prepared, and sites that pass inspections with confidence.
Whether you need a one-time audit, ongoing compliance support, or help fixing repeat violations, Apt is built to handle the job—on-site, online, or on-call.
What We Offer
Third-Party Environmental Audits
We conduct full-scale compliance and ISO-aligned audits, tailored to your facility type, industry, and region. You’ll get clear reports, risk-ranked findings, and a step-by-step action plan.
Pre-Audit Assessments & Gap Analysis
We help you identify and fix issues before regulators arrive—from expired permits to missing training logs. Our team is trained to catch what most internal reviews miss.
Corrective Action Support
Findings are just the start. We roll up our sleeves and help you fix what matters—labelling, documentation, training, waste storage, reporting, and more.
EHS Management System Design
Need a repeatable system to track it all? We help you build or refine your EHS Management System so you’re ready for ISO 14001, 45001, or corporate ESG audits.
Long-Term Compliance Programs
For companies managing multiple sites or long-term risk, we offer contract-based EHS leadership and consulting—from project setup to monthly audits.
Why Companies Choose Apt
- 20+ years of hands-on EHS expertise
- Specialists in energy, chemicals, agriculture, and manufacturing
- Responsive, field-tested consultants—not just report writers
- Fully customized audits, training, and remediation plans
- National reach with local familiarity—offices in Washington, Texas, and Idaho
Ready to Stay Ahead of the Curve?
Don’t wait for a violation to take action. Let’s get you audit-ready—now and for the future.
Email: info@aptsol.net
Call: 1-360-299-6666
Request an Audit Consultation
Ready to Schedule Your Environmental Audit?
You don’t need to wait for a surprise inspection or a compliance notice to take control of your environmental performance.
Whether you're operating a single facility or managing multiple sites across high-risk industries, an environmental audit gives you the insight and confidence to do things right—from permits to processes to people.
At Apt Environmental Solutions, we help you go beyond the checklist. We help you build systems, lead teams, and prepare for inspections—without fear, confusion, or delays.
Explore More
- Environmental Audit Services
- Environmental Compliance Guide
- Case Study: Audit Success at a Chemical Plant.
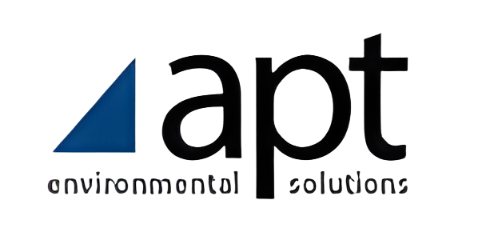
Get in touch